The TRUSSDECK™ Ultimate Building Block System and Process
TRUSSDECK™ Building Block Systems is a science and engineering group dedicated to delivering
the latest technologies in materials science and
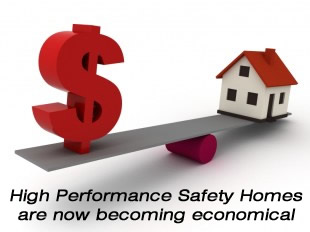
chemical technology
to the building and construction industries. Our research laboratory continually develops new innovative high performance
materials which range from ballistic catching polymer materials to extreme longevity polymer coatings to sustain lifetime wear in harsh
environments. Please read our
Science-Technology web page as we discuss
developing our advanced technologies. In this section, we want you to learn about how we utilize this technology to bring about high
performance safety building structures for use in the protection of our homes and workplaces where we live our lives. It has become
apparent that residential homes and other safety building structures for people everywhere in today's volatile world must be addressed
by the use of today's technology. As the age of depleting our oxygen supplying tree resources is coming to an end and
people's safety becoming a priority in this world while also in the light of protecting our families we must now turn to creating
these energy efficient safety structures economically. Implementation of these advanced materials within an economical forum is the now
the global theme where we must all contribute to the world in
which we our lives and for the generations of lives to come on this planet.
Research, development and engineering groups all over the world produce our world's
technological developments which include these
necessary high performance materials for our future. These types of materials are the key to building the new generation of safety
energy efficient building structures we are in need of today. The required physical properties of these materials are now in high
demand in every aspect of our lives. Our science and engineering groups at Trussdeck USA have worked in collaboration with numerous others
to produce these much more economical extreme property materials (Video clip Right). These new extreme property materials include being
fire retardant, waterproof, hurricane & tornadic wind resilient, high impact resistant, solar heat cooling, insect proof, thermally
energy efficient, acoustically quiet, surge water resilient and earthquake seismic wave isolating. Trussdeck structural safety building
assemblies deliver the inherent extreme performance, longevity and maintenance free
attributes we are all demanding. Our future home investment should be out with the old and in the new. The value of these new home and
other safety building structures with last over time. Trussdeck Building Block Systems are creating these assemblies for all people
around the globe, licensing the technology to countries to set up their own factories and employ their own people to construct safety
structures.
Trussdeck™ Structures: The first understanding is to know what are Trussdeck™ Safety Building
Structures... where are they best
used ...and what are their limitations. Trussdeck's are structural high performance building blocks used in the construction of
structural safety assemblies such as residential homes, school houses, activity centers, small to medium sized business buildings,
storefronts, fast-assembly military and nursing buildings, environmental safety shelters, protective enclosures and other types of
structures where protection is needed for people to live and work. The individual Trussdeck Building Blocks become unitized into a
structural bonded and bolted energy handling assembly. Trussdeck buildings may be designed in just about any geometrical
configuration. Limitations of the Trussdeck Building system are to the point where concrete and steel take over such as for
larger building structures. Limitations also exist depending on the level of protection regarding high
levels of ballistic and explosion performance. Trussdeck possesses the composite technology to integrate these extreme protective
features into a Trussdeck assembly but the economics become skyrocketing. For these high levels of protection it is best to utilize
steel reinforced blast shield protected concrete structures.
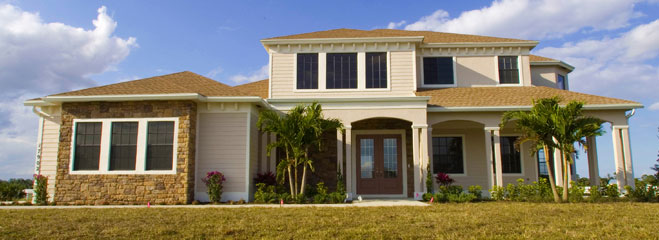 |
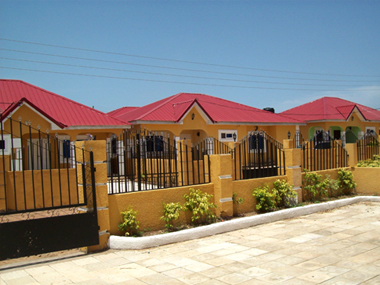 |
The Trussdeck™ Building Process
Start to Finish -- Step 1: Determine all desired interior and exterior design requirements as normally created in
a full set of building plans. List the degree of structural loading forces exerted from mother nature's environmental conditions.
List any areas of the floor plan where heavier than normal weight loads may occur such as walk in freezers, large body of water,
heavier equipment and weight rooms. These combined building requirements are termed the Trussdeck Assembly Criteria (TAC). Next,
our central engineering group develops the structural computer model of the specific design. After the model has been created the
Analytical Group takes over.
The engineer's model is subjected to the realistic physical static and dynamic loading conditions
as prescribed in the TAC. As an example, let's say the TAC dictates the building is located in a tropical wind CAT 4 environment,
110F temperature environment and susceptible to low surge water flooding. These combined loading conditions are given boundary
conditions which then are numerically computed to generate a dynamic simulation showing the level of strength and weakness values
of the structural assembly. Trussdeck engineering works directly with the analysis group to finally optimize
the structural design. After completion, engineering complies the materials build list which is then will be forwarded to
manufacturing. Every new Trussdeck building design given its own TAC set is analyzed in this method. After engineering closure,
the set of building plans The construction assembly is forwarded to the destination's local building Inspection engineer for
agreement on construction.
Trussdeck™ Manufacturing -- Step 2: After all is confirmed the Trussdeck components
are manufactured. All Trussdeck components are double-checked for dimensional accuracy as so all in accordance to the design
build GD&T tolerances. All Trussdecks are then series marked and color-coded with its own individual structural and positioning
designations. All Trussdecks are then checked carefully by plant engineering to align within the correct "Material
Build Stack" (MBS) and assure all parts are properly marked prior to shipping. All assembly materials, assembly
fixtures, special components and required tools for the particular Trussdeck Structural Build Unit (TBU) are checked and
forwarded to the supervisor of the
Installation Team. All members of the installation team are factory
certified with cross-functionality training.
Trussdeck Installation -- Step 3: All Installation Teams (ITs) are notified with a
prior 2 week assembly notice for every TBU in which they are responsible. Prior to the Trussdeck™ Building Blocks and
Installation team arrival, the Foundation Building Team (FTs) prepares the site with the complete foundation installation.
The IT supervisor is also responsible for the FT work. He is normally the focal point of contact for the entire TBU to the
customer and the local building inspectors. FT and IT
supervisors must both sign off with each other in accordance with the job's design engineer specification. Any on-site
change must be submitted with full documentation as per Trussdeck ISO standards to central engineering. Once the FT and IT
nd approval from the
local building inspection department is signed off only then will ground breaking commence. The foundation build is the most
important and critical build stage for the construction of the
TBU. Normally, Trussdeck installations are completed within 1-2 weeks*. All Trussdeck™ Building Blocks are bonded and bolted to
each outer creating a unified body assembly which permits imparting transient forces to be transferred efficiently throughout
the structure.
Trussdeck Building Inspection -- Step 4: Normally in a building process using
conventional building materials there are many intermittent before/after step inspections, sometimes 10-12 or more.
Trussdeck buildings normally only require just a few. Before any breaking ground, the Trussdeck™ system is reviewed
with the local inspection department and the material and construction of the Trussdeck system is thoroughly reviewed
so there is no confusion for them with this new type of construction when it it installed. The first inspection is
inspection of the footing excavation, soil compactness, drainage, waste, in ground plumbing, electrical service, etc.
The second is after the foundation is complete ready for Trussdeck installation. At this point is where 10+ normal
inspections are omitted. These are associated with before and after rough in build, insulation, plumbing, electrical,
HVAC, etc. Trussdeck is normally inspected 1 more time at final.
Other Trussdeck™ Structures:
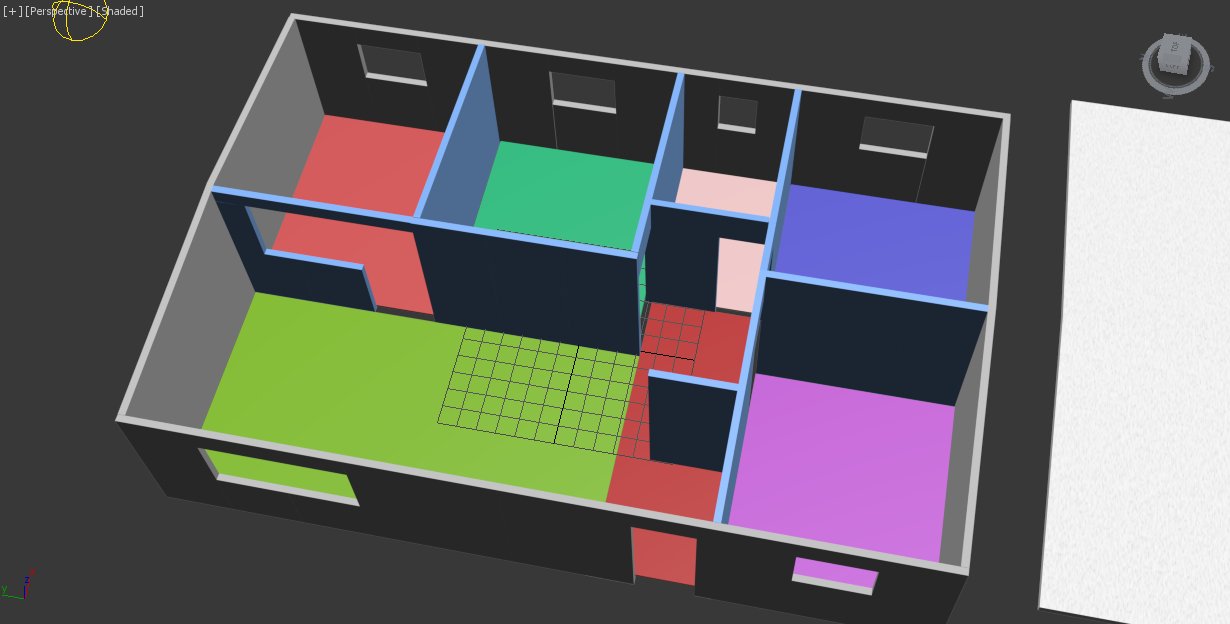 |
|
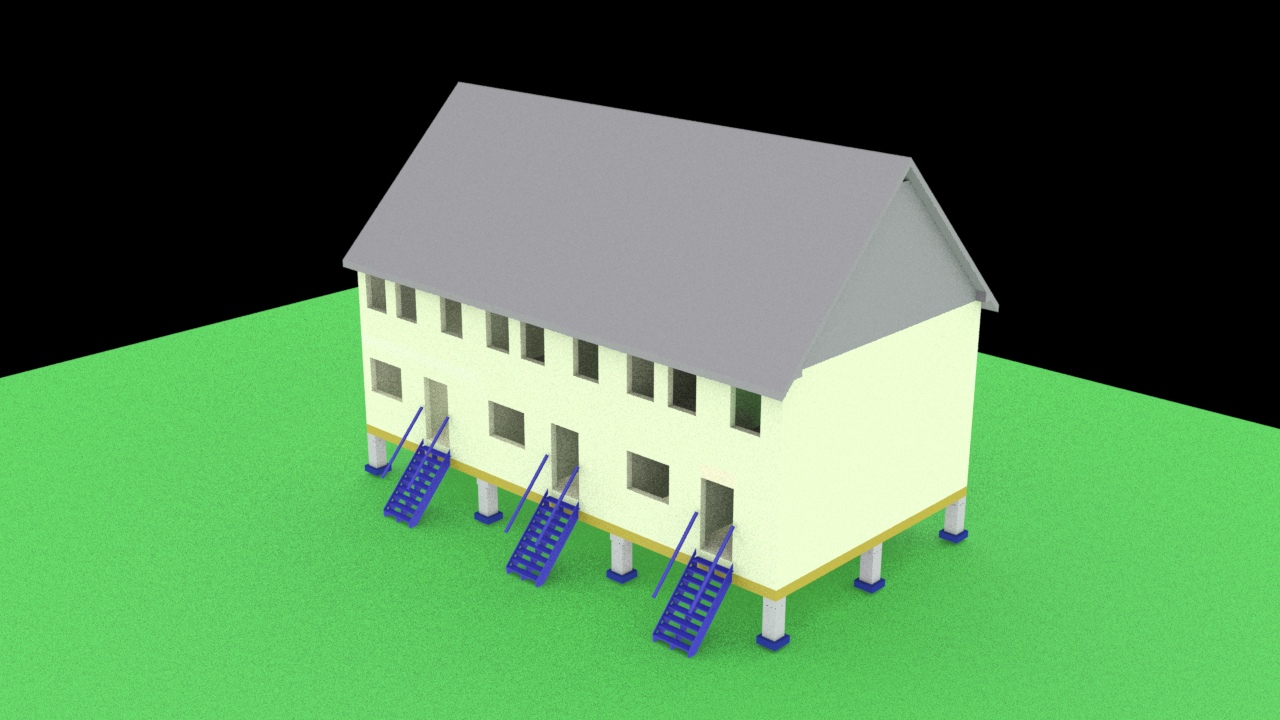 |
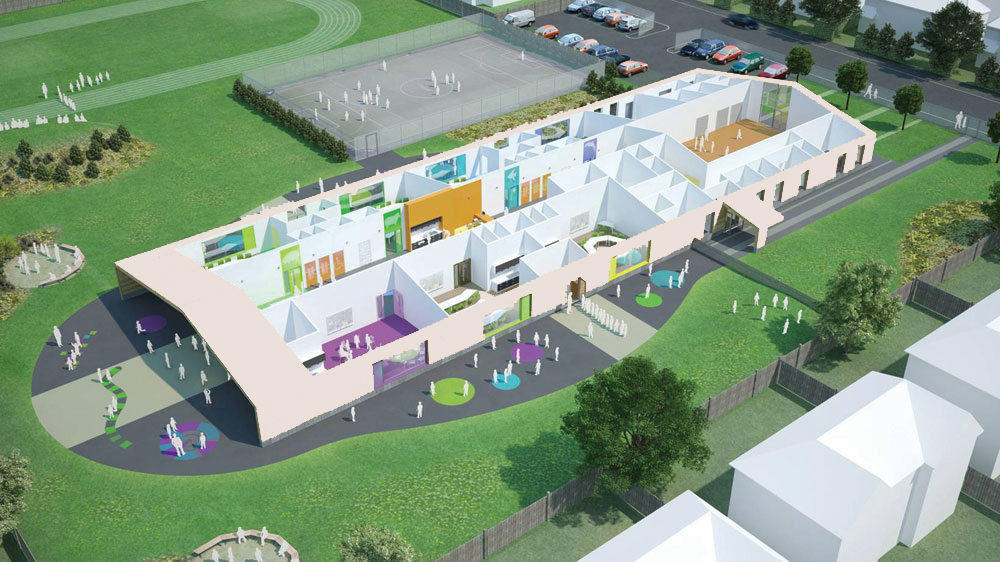 |
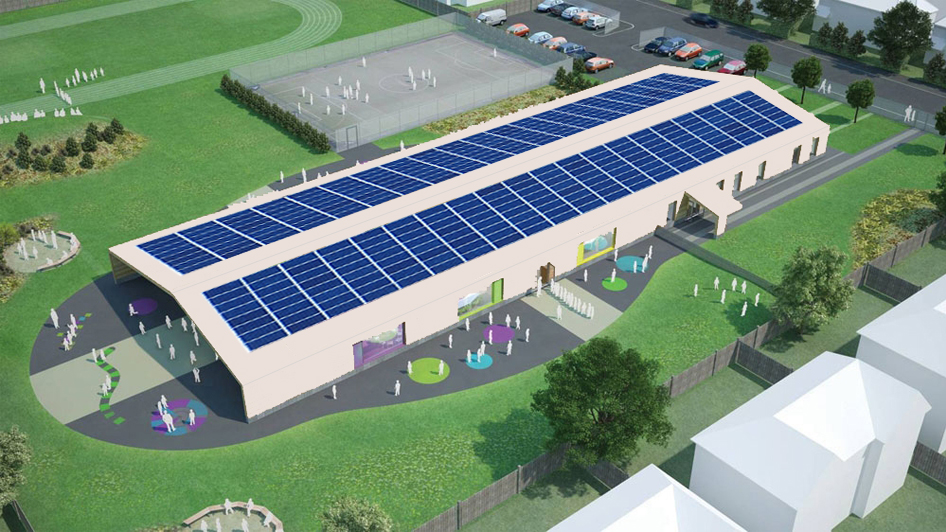 |
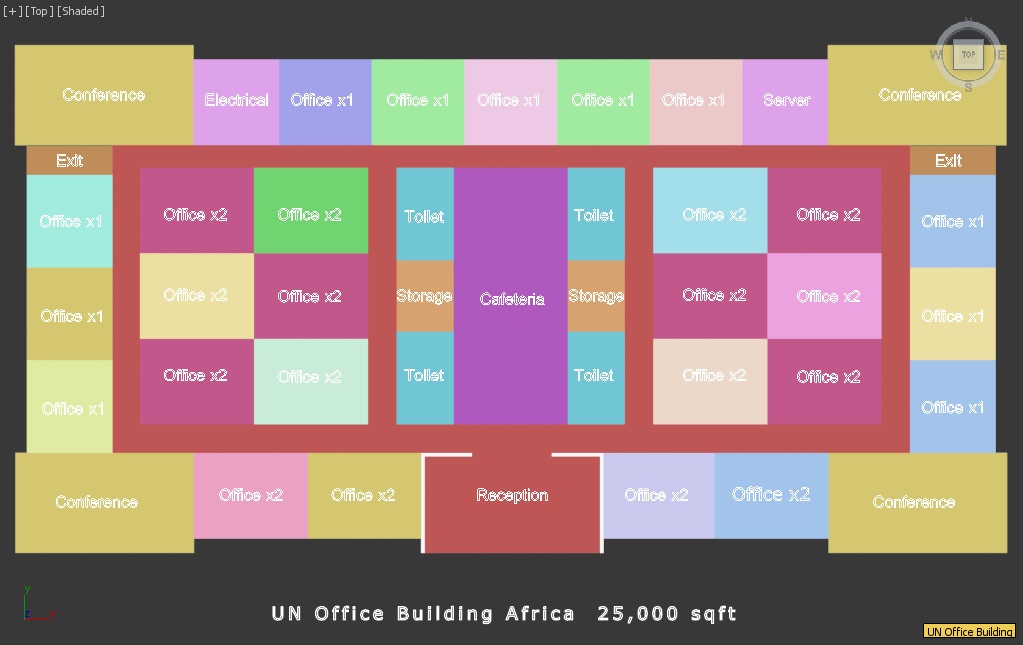 |
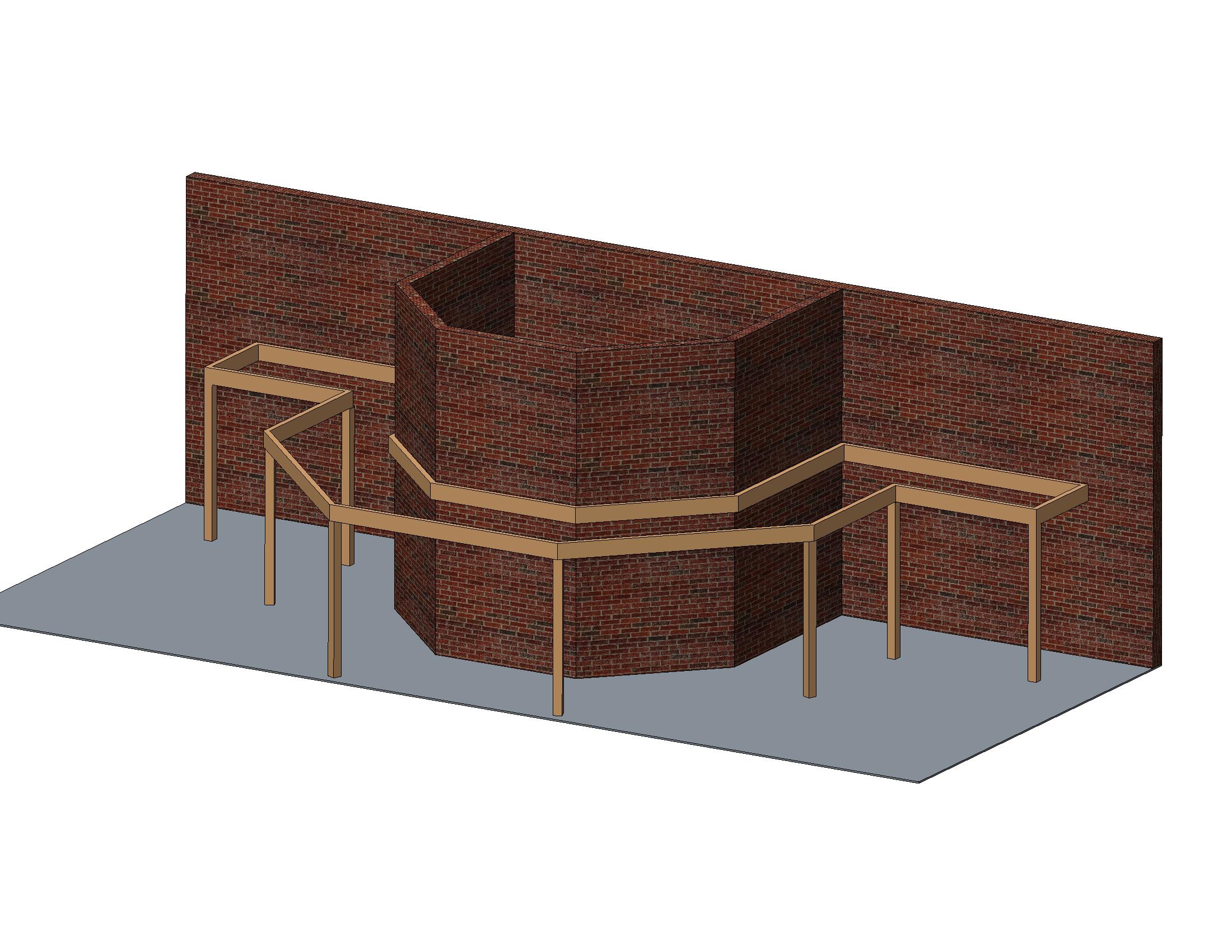 |
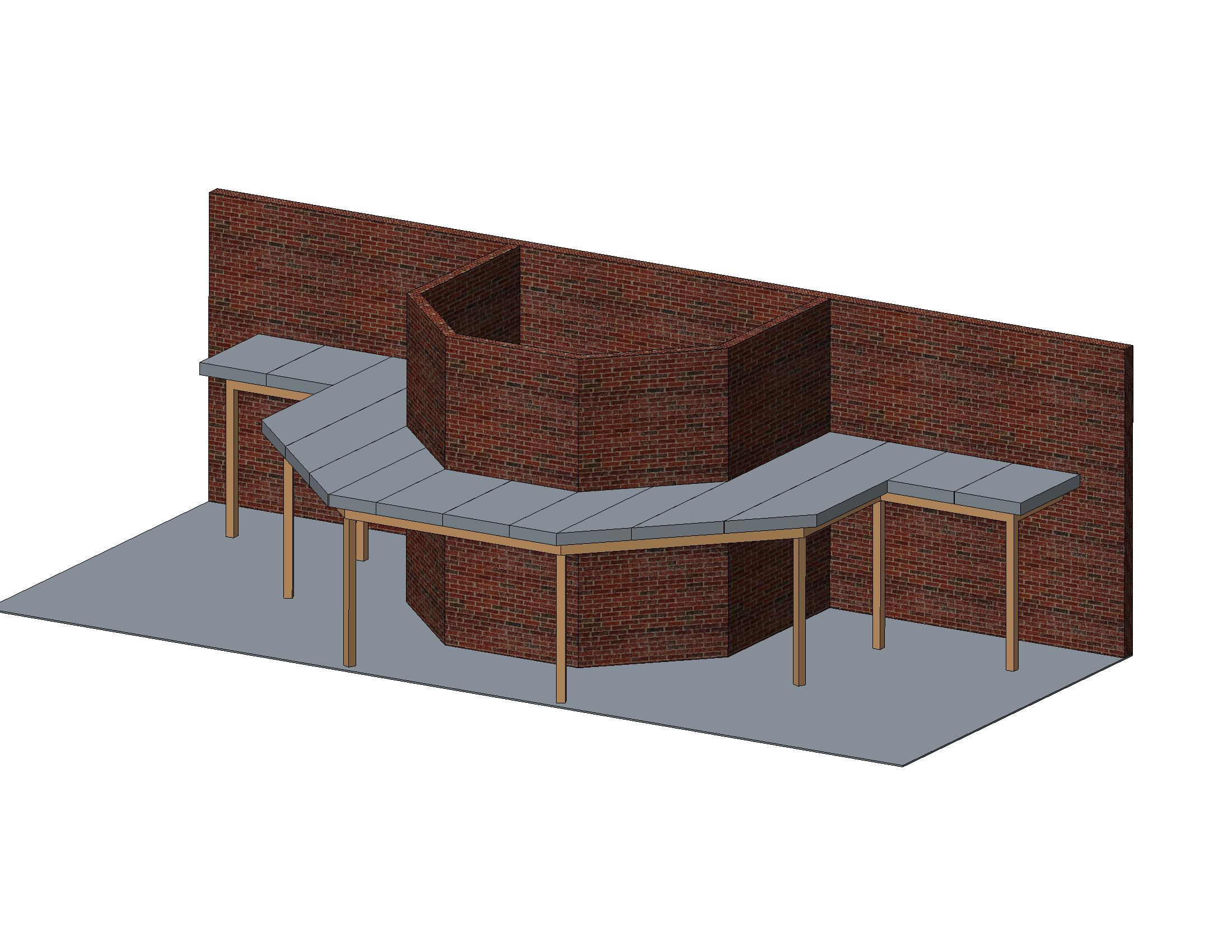 |
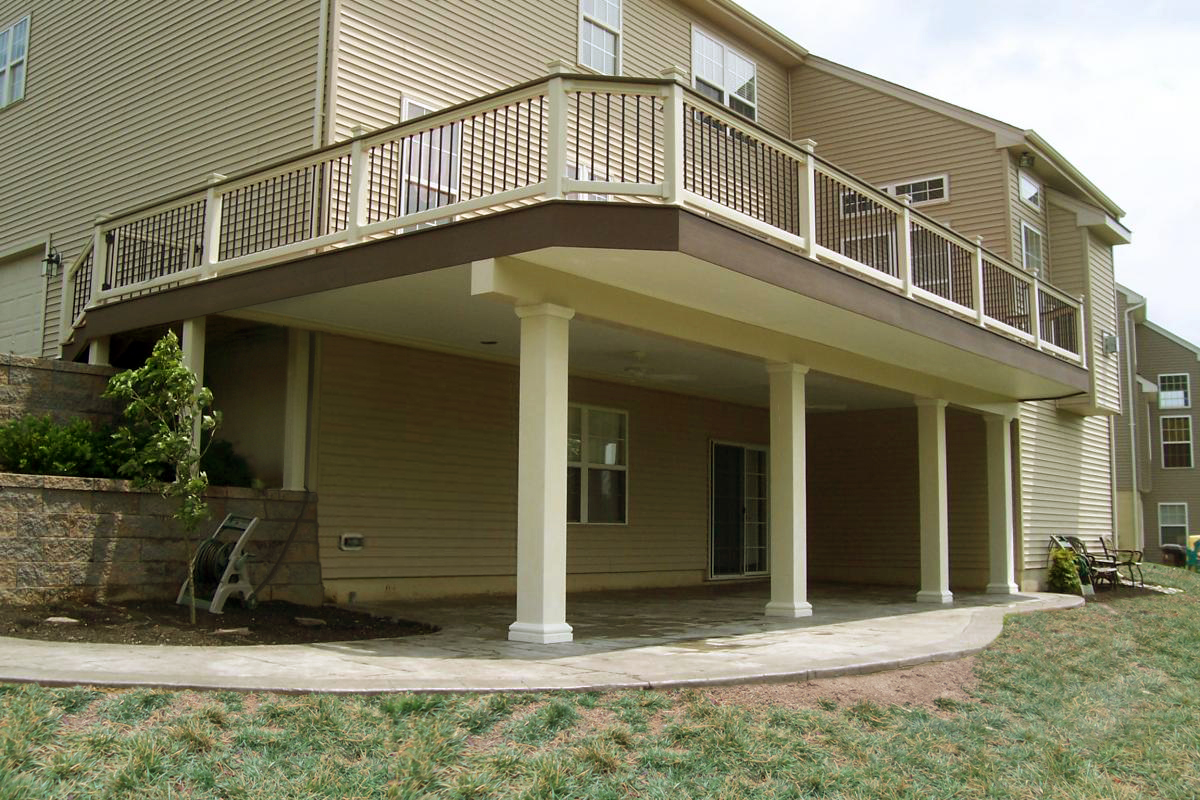 |
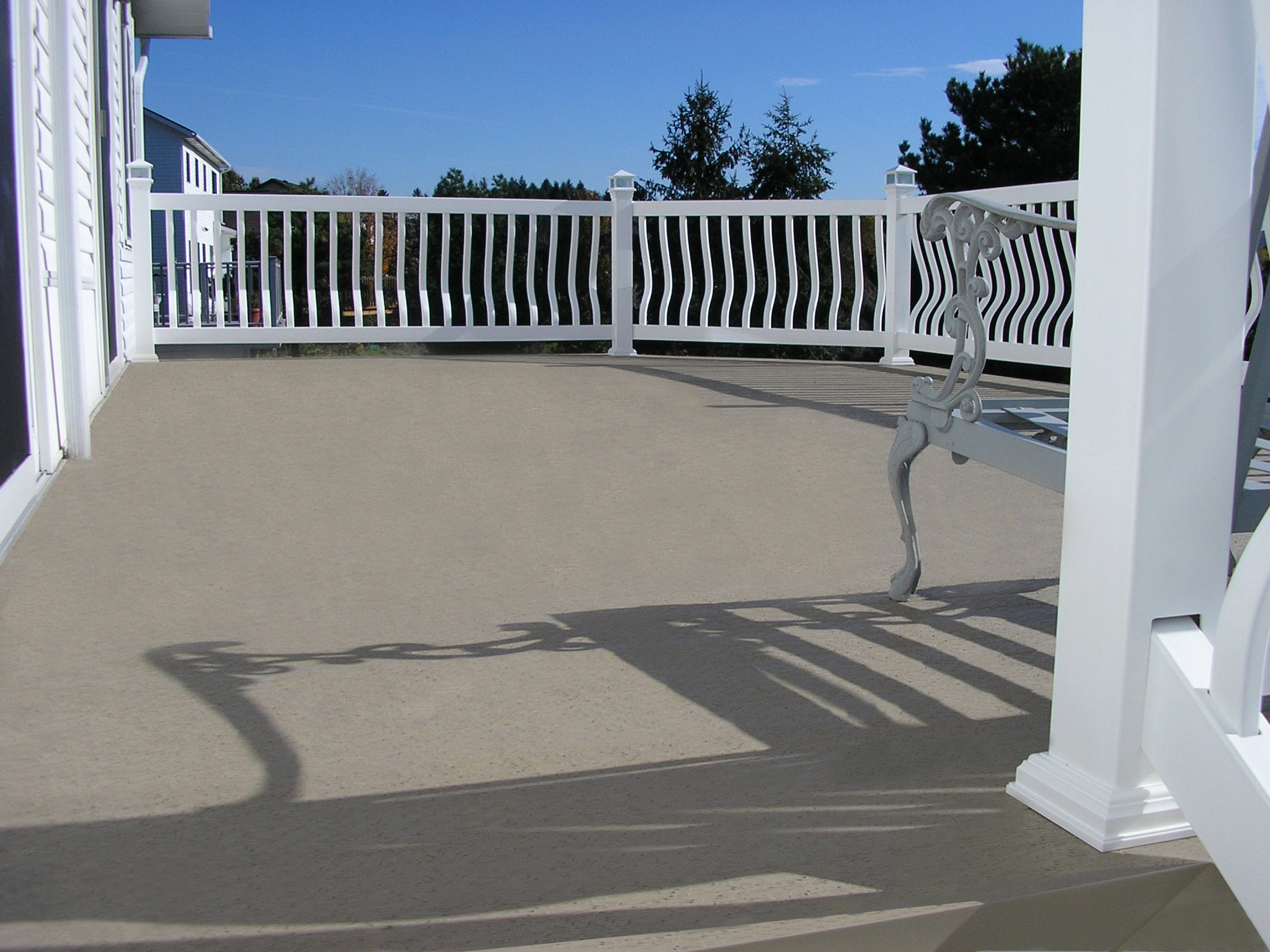 |
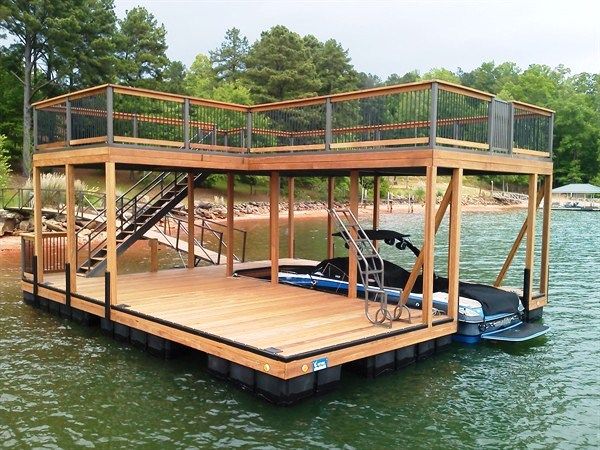 |
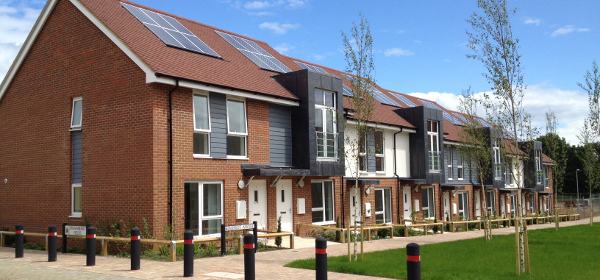 |
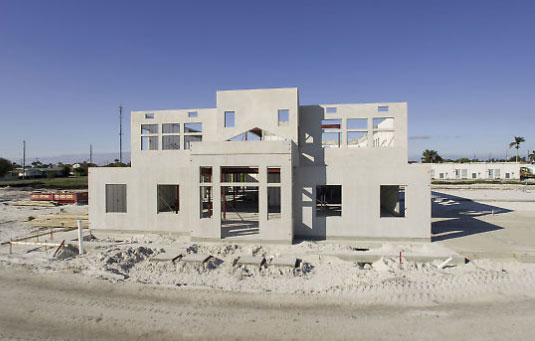 |
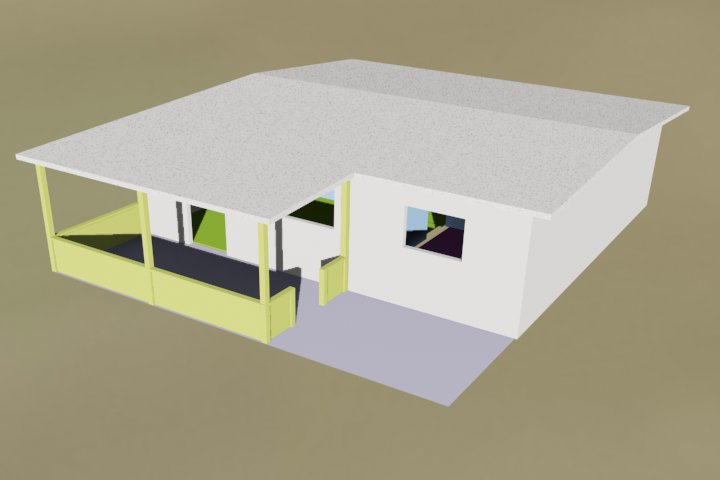 |
|